Wall to Wall reduces CO2 emissions at every stage
When it comes to sustainability, what people really want to know is what you are doing right now.
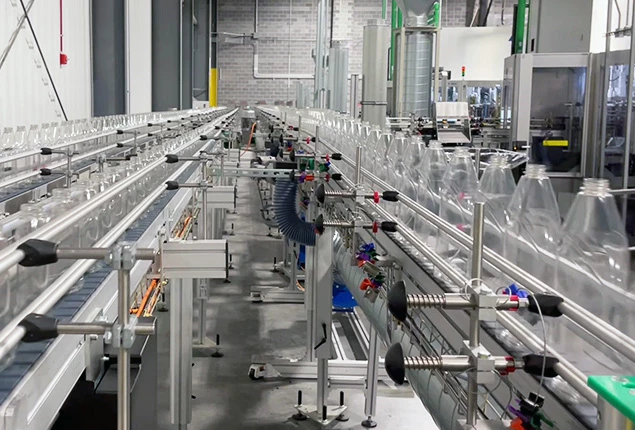
Shifting from remote packaging production to embedded, wall to wall manufacturing with Logoplaste makes an immediate impact on your carbon footprint and your bottom line.
Savings that help save the planet
Six ways embedded, wall to wall packaging plants cut your carbon footprint and make your business more efficient
An embedded Logoplaste plant delivers bottles directly into your filling lines, no trucking, no shipping of empty bottles.
The CO2 impact of eliminating freight adds up fast. If we calculate the average CO2 emissions avoided by our wall to wall business model as well as nearby sites, this will represent -14,962* tons of CO2 per year, the equivalent to 8,500 flights a year from London to New York on a Boeing 747.
Offsetting that much CO2 would require 686,000 trees a year, every year.
*Logoplaste 2020 internal study
If you don’t need to ship bottles, you don’t need to pack them. That means no more boxes, totes, gaylords, tape, stickers, bags, shrink-wrap. Secondary packaging goes away.
There is no need for extra material, no need to hire someone to pack and unpack. Embedding packaging manufacturing inside your operation reduces energy consumption, lowers machinery maintenance, and lowers your operating costs.
Filling and capping the bottles within minutes of manufacturing them provides structural support to the bottles, allowing us to use less plastic. Bottles made off-site have to be thicker to survive loading, transportation, and unloading.
But not all lightweight programs are right weight programs. At Logoplaste we implement right-weight to ensure we protect the product, fulfilling quality and safety standards and to guarantee we are in line with recyclers’ requirements, so packaging can be easily sorted and recycled, which makes your products a better match for bottle to bottle programs.
With wall to wall, packaging production ramps up and down in sync with your operation, eliminating packaging inventory. Empty packaging never sits in a warehouse waiting for demand and your filling lines never wait for bottles to arrive.
It’s a single, seamless production line from us to you - true elegance in motion.
Wall to wall means two manufacturing plants in a single facility for less duplication and lighter impact.
We can retrofit existing facilities with minimal additional power, water, and sewage infrastructure. Building new co-located facilities allows us to work with customers to design facilities that are fiscally and environmentally more sustainable.
Embedded, wall to wall manufacturing puts an entire packaging plant at your disposal. You never get bumped for another company’s production run.
Co-locating also demands we work side by side in constant communication. To succeed we have to define common goals and share critical values around timeliness, safety, and quality. This level of dedication and coordination pays dividends across the operation. Things get done better, faster, and far more efficiently.
Wall to wall is our foundation for the next revolution in CO2 emissions reduction.
Our next generation of plants will begin our transition to carbon neutral and regenerative facilities.
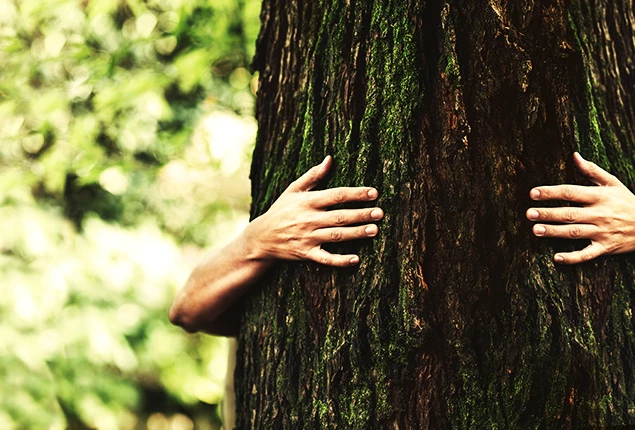
Logoplaste relies heavily on energy to produce plastic packaging. Responsible energy is our current baseline as we implement improvements to optimize our efficiency.
Energy upgrades - 2020 and ongoing
- 100% Renewable-sourced energy at Logoplaste Pomezia (Italy) and Logoplaste Dumfries (UK)
- Solar PV panels installed at Logoplaste Mealhada (Portugal) and Masterchem (Poland)
We conduct regular energy assessments and constantly update our machinery, auxiliary equipment, lighting and facilities. In 2020 Logoplaste appointed full time person to focus on energy efficiency initiatives across all of our facilities to ensure a consistent path towards efficiency.
Our current energy reduction strategies include lighting efficiency, waste heat recovery, plus machine and utilities optimization. We’re transitioning to renewable energy for our sites through global power purchasing agreements and the installation of photovoltaic panels on our facilities.
Using recycled plastic resins, instead of virgin resin, to manufacture new plastic packaging is critical to reduce the amount of carbon we consume and the amount of plastic in the environment.
Logoplaste is actively pushing, together with our clients, for the accelerated incorporation of recycled materials and educating our partners on how to make packaging sustainable.
The case for using recycled materials is absolutely clear:
- It reduces the need for virgin, fossil-based raw materials
- It saves energy
- It diverts waste from landfills
- It reduces our carbon footprint
Logoplaste has been using recycled raw materials in our products for over 10 years, for food and non-food applications. Some of our packaging is produced with 100% recycled content.
Each plastic material - HDPE, PET - has its own production, recycling, and environmental consequences, which makes choosing the right materials for our packaging critical. While our clients are the ultimate decision makers in the choice of materials, Logoplaste has proven the economic and aesthetic viability of 100% recycled, 100% recyclable, bottle-to-bottle manufacturing.
"For us at Racine, it is a source of great pride to say all our bottles are produced with recycled content. We feel that we contribute towards a Circular Economy, where plastic is not perceived as waste, but as a valuable resource that is reused.
My team and I are pleased to work for a better, more sustainable world."
LOUIS BELL | Plant Manager
Logoplaste Racine, USA